A pristine floor has the power to completely transform the ambiance of any space, providing a visual upgrade; however, achieving that high-end finish can often feel like a distant dream. What if it were possible to attain a showroom-quality floor in just a few straightforward steps?
This guide outlines the essential process of applying polyurea polyaspartic floor coatings, including everything from surface preparation to the final inspection, using high-quality and professional-grade tools.
Whether you are a DIY enthusiast or contemplating professional assistance, this guide will help you understand why this durable solution, featured in Polyurea Polyaspartic Atlanta, GA, could be your pathway to a stunning and long-lasting floor.
This installation guide emphasizes cost durability and customer satisfaction.
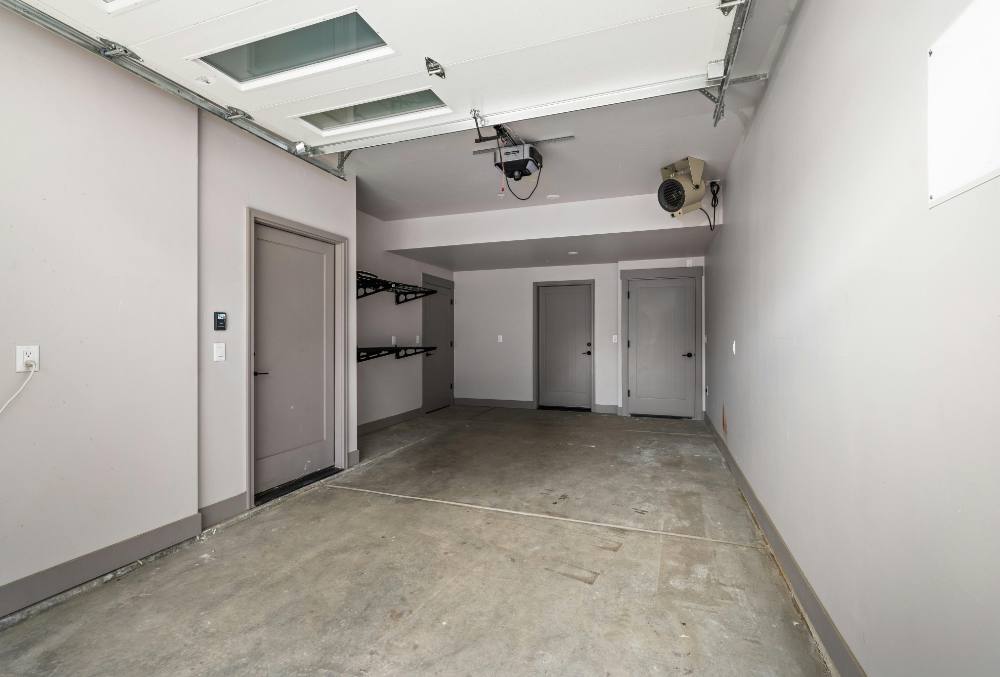
Preparing the Surface for Coating: An Essential Step in Garage Floor Installations
Preparing the surface for coating is an essential step in the installation of polyurea polyaspartic floor coatings, especially in garage spaces that frequently experience moisture issues, wear, and dirt buildup.
For homeowners considering concrete floor refinishing in Atlanta, it’s important to ensure a clean and even concrete surface, as this is key to achieving a strong bond with the final coating, ultimately enhancing its durability and performance.
This preparation process includes thorough cleaning, addressing any necessary repairs, and assessing the overall condition of the surface to maximize the effectiveness of the coating application.
Applying the Primer: A Comparison with Epoxy Alternatives
Applying a primer is an essential step that significantly enhances the surface bond and ensures optimal performance and durability when installing polyurea polyaspartic floor coatings.
There are various types of primers available, each tailored to address different surface conditions and materials.
For example, epoxy primers excel on concrete surfaces due to their strong adhesion properties, while acrylic primers are versatile and dry quickly, allowing for faster application of the coating. It is important to ensure that the surface is clean and free of debris before applying any primer.
The application process typically involves the following steps:
- Preparing the surface by cleaning and repairing any imperfections.
- Mixing the primer according to the manufacturer’s instructions.
- Applying an even coat using a roller or brush, making sure all areas are thoroughly covered.
This preparatory step is crucial because a proper primer not only enhances adhesion but also helps mitigate issues related to moisture infiltration. This significantly contributes to the coating’s overall durability and longevity.
By effectively sealing the substrate, the primer creates a barrier that can withstand wear and tear, ultimately saving time and resources in maintenance.
Mixing the Polyurea and Polyaspartic Components: Ensuring Chemical Resistance
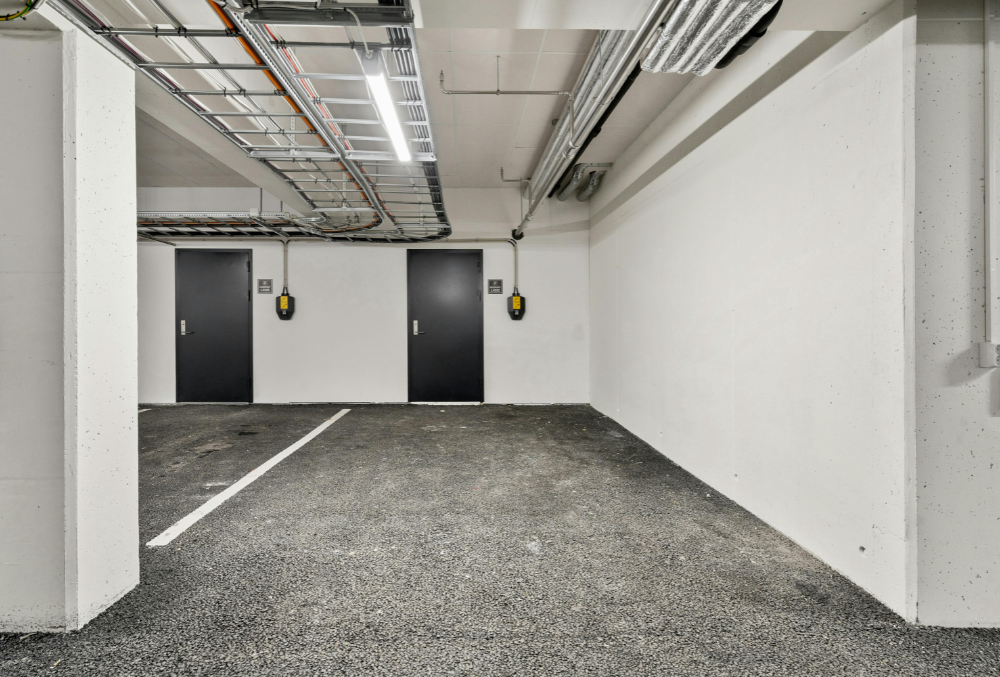
Accurate mixing of the polyurea and polyaspartic components is essential for achieving the desired properties of chemical resistance and durability in your garage floor coating.
To ensure a successful blend, it is important to pay close attention to the precise mixing ratios specified by the manufacturer, which typically range from a 2:1 to a 4:1 ratio of component A to component B. Having the right tools is equally critical in this process; a high-quality mixing paddle attached to a power drill is recommended to achieve a homogeneous mixture.
Employing techniques such as mixing in a clean bucket and scraping down the sides will aid in reaching a uniform consistency. It is paramount to adhere strictly to the manufacturer’s instructions, as doing so not only guarantees optimal performance but also enhances the longevity of the coating, ultimately protecting your investment.
By following these guidelines, you can achieve a flawless finish for your garage floor.
Applying the Base Coat: The Foundation of Coating Comparison
Applying the base coat is a crucial step in the installation of polyurea polyaspartic floor coatings. It not only provides a smooth finish but also serves as the foundation for the additional layers.
This initial layer enhances the aesthetic appeal of the floor while also playing a vital role in its long-term durability.
To achieve an even application of the base coat, it is important to use a roller or sprayer, ensuring consistent pressure throughout the process. Begin at one corner of the garage and work systematically to avoid overlaps. For edges and tight spots, a brush can be quite helpful to ensure that no areas are left bare.
Once the base coat is applied, allow it to cure properly. This typically involves maintaining specific temperature and humidity levels to ensure that the base coat bonds effectively with the substrate, thereby enhancing the overall performance of the garage floor.
When executed correctly, this foundational layer significantly contributes to the longevity and resilience of the entire flooring system. This makes it essential for homeowners who are investing in a durable finish.
Adding Decorative Vinyl Flakes: Aesthetic and Safety Features
Adding decorative vinyl flakes is an optional yet popular enhancement that can significantly elevate the visual appeal and aesthetics of your garage floor coating.
These attractive chips not only provide a stunning finish but also serve practical purposes that contribute to the flooring’s longevity and safety. When integrated into the coating process, decorative chips can create a textured surface, which enhances slip resistance and reduces the likelihood of accidents.
There are numerous options available, ranging from vibrant colors to muted shades, allowing individuals to customize their garage floors to match personal tastes or existing decor.
To apply these flakes effectively, they can be sprinkled onto the wet coating, ensuring an even distribution for a uniform appearance. This approach not only enhances the flooring’s look but also reinforces its durability against wear and tear.
Applying the Clear Topcoat: Achieving a High-Gloss Finish
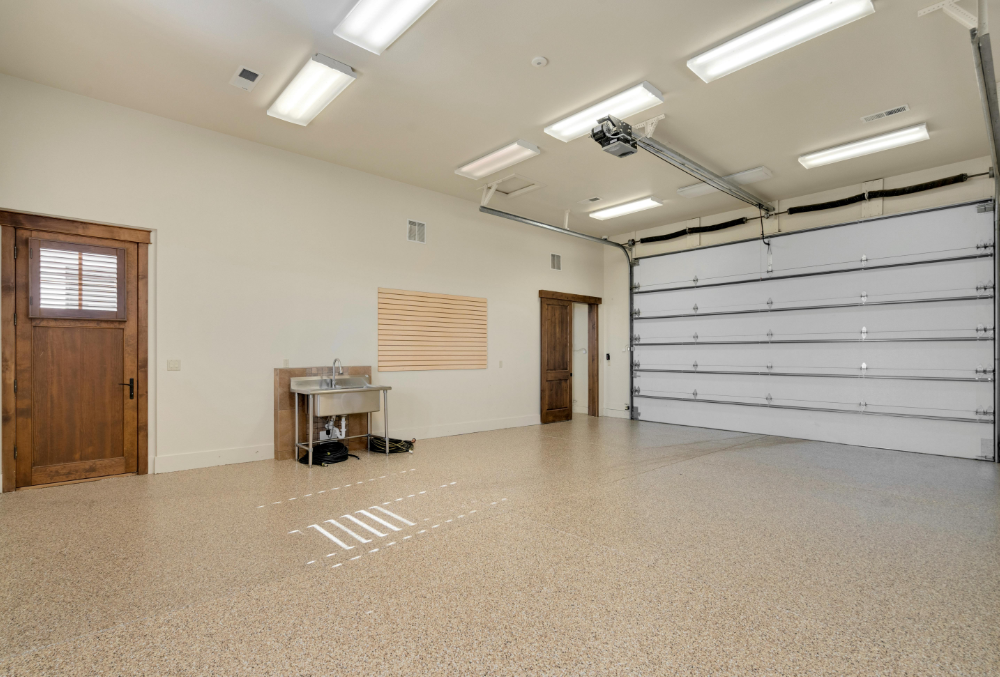
The application of a clear topcoat is essential for safeguarding your polyurea polyaspartic floor coating. It not only provides a high-gloss finish but also ensures UV stability and enhances chemical resistance.
Regarding quality flooring, maintaining durability and visual appeal is of utmost importance. This is where the clear topcoat comes into play. It serves as a durable shield against scratches and stains while simultaneously enhancing the color and depth of the underlying coating.
By applying an even coat, you can prevent unsightly imperfections that may detract from the overall appearance of the floor.
To achieve a flawless application, start by thoroughly cleaning the surface to eliminate any debris or dust. Using a high-quality roller or sprayer will help you distribute the coating evenly. Furthermore, pay special attention to edges and corners, using a brush as needed for precision.
Allowing the recommended curing time is crucial. Generally, a period of 24 hours is advised to ensure that the topcoat bonds effectively, maximizing both its protective qualities and aesthetic appeal.
Letting the Coating Cure: Optimizing Curing Time
Allowing the coating to cure properly is essential for maximizing the performance and durability of your polyurea polyaspartic floor coating.
Effective curing is crucial as it ensures that the coating bonds adequately to the substrate, which helps prevent issues such as peeling or chipping in the future.
Various factors, including temperature and humidity, significantly influence the curing process. For example, warmer temperatures can expedite curing times, while high humidity levels may prolong them.
Optimizing these conditions is important for achieving the best results. Here are some recommended curing times based on different conditions:
- Ideal Temperature (70°F-80°F): 24 hours for light traffic, 72 hours for heavy traffic.
- Cooler Conditions (below 60°F): Allow for an additional 12-24 hours for proper curing.
- High Humidity (above 70%): Be prepared for potential delays and longer wait times.
To ensure effective curing, it is advisable to maintain stable environmental conditions, avoid heavy foot traffic during the initial curing phase, and always adhere to the manufacturer’s instructions for best practices.
Checking for Any Imperfections: Ensuring Customer Satisfaction
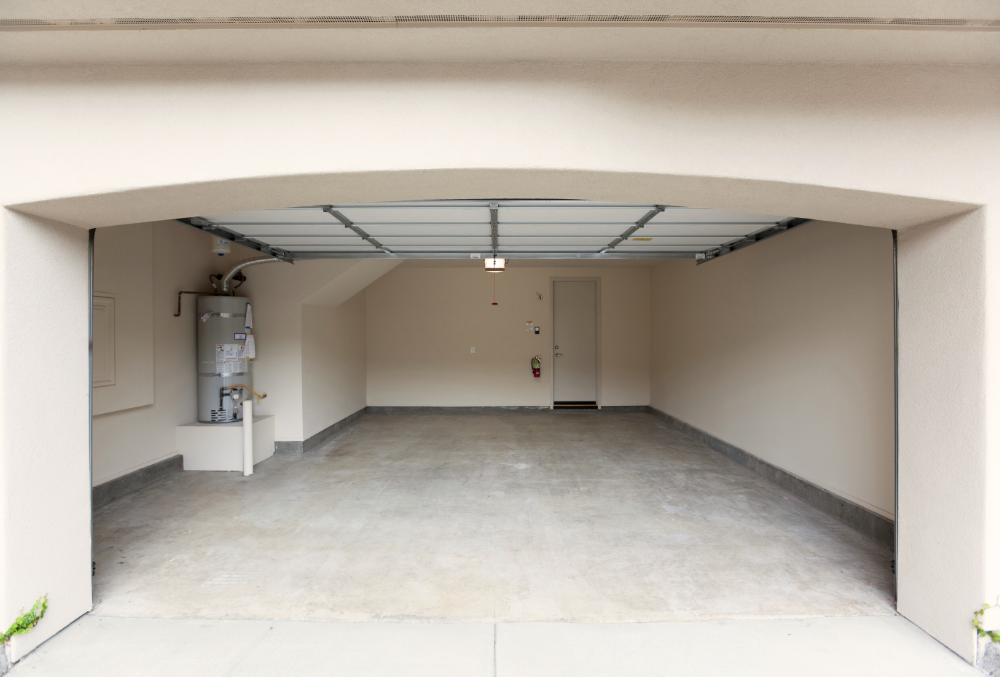
Checking for any imperfections after the coating has cured is a vital step in the installation process, as it ensures the quality and longevity of your garage floor.
When inspecting the finished surface, it is essential to pay close attention to detail, as any flaws could compromise the integrity of the coating. For instance, be on the lookout for bubbles that may have formed during application, as these can indicate improper adhesion.
Additionally, consider the following points during your inspection:
- Look for signs of unevenness, as this can lead to both aesthetic and functional issues.
- Discoloration is another critical factor to note; it may suggest that the materials were not mixed properly or were exposed to moisture before curing.
Addressing each of these factors during the inspection phase is crucial for maintaining quality assurance and risk management. This diligence will significantly impact the overall performance and appearance of the garage floor, ultimately saving time and money on potential repairs in the future.
Touching Up as Needed
Addressing any areas that require attention is crucial for maintaining the visual appeal, improvement, and integrity of your polyurea polyaspartic floor coating.
To achieve a flawless finish, it is essential to gather the appropriate materials prior to beginning the touch-up process. You will need a quality touch-up kit specifically designed for this type of coating, a clean cloth, a fine-bristle brush, and possibly some sandpaper to smooth out any rough spots.
Start by thoroughly cleaning the area to remove any dirt and debris, as this will enhance the adherence of the new coating. Once the area is dry, apply the touch-up coating with the brush, ensuring you create a thin, even layer that matches the existing finish.
Regular maintenance, including cleaning and conducting periodic inspections, will help prolong the life of the coating and keep it looking its best. Therefore, establishing a schedule for maintenance checks is highly recommended to identify any potential issues early on.
Cleaning Up and Removing Any Tape or Protection: A Maintenance Process
Cleaning up and removing any tape or protective coverings after the installation of your polyurea polyaspartic floor coating is an essential final step in garage floor coatings Atlanta. This ensures a polished finish and prepares the area for immediate use.
Taking the time to do this correctly not only enhances the overall appearance but also contributes to the longevity and durability of the surface. After installation, begin by carefully peeling off any protective coverings or tape.
It is advisable to do this slowly and at a 45-degree angle to prevent any damage to the edges of the coating. Be vigilant for any residual adhesive that may remain, as this could interfere with the coating’s integrity.
Following that, conduct a thorough inspection of the area. Look for any stray materials, such as dust, debris, or loose particles that could negatively affect the finish.
This step is crucial for ensuring the optimal performance of the coating. Removing these materials can help achieve a flawless result and prevent potential issues down the line.
Inspecting the Finished Coating: Ensuring UV Stable Quality
Inspecting the finished coating is an essential step in ensuring that the polyurea polyaspartic floor coating has been successfully applied and meets quality assurance standards, with UV exposure considerations.
When evaluating a newly coated floor, several critical aspects warrant consideration. A thorough inspection will help safeguard the longevity and functionality of the floor, leading to a satisfactory end result. Here’s a practical checklist:
- Surface Smoothness: Run your hand over the surface to feel for any bumps or irregularities that may impact the overall finish, especially in residential settings.
- Adhesion: Scrape a small area to confirm that the coating has properly bonded to the substrate. Good adhesion is essential for durability.
- Cosmetic Flaws: Look for discoloration, bubbles, or uneven texture, as these can detract from the visual appeal of the coating.
By carefully examining each of these elements, one can assess whether the floor is equipped to withstand wear and tear, ultimately enhancing its performance and lifespan.
Benefits of Polyurea Polyaspartic Floor Coatings: Value Investment Opportunities
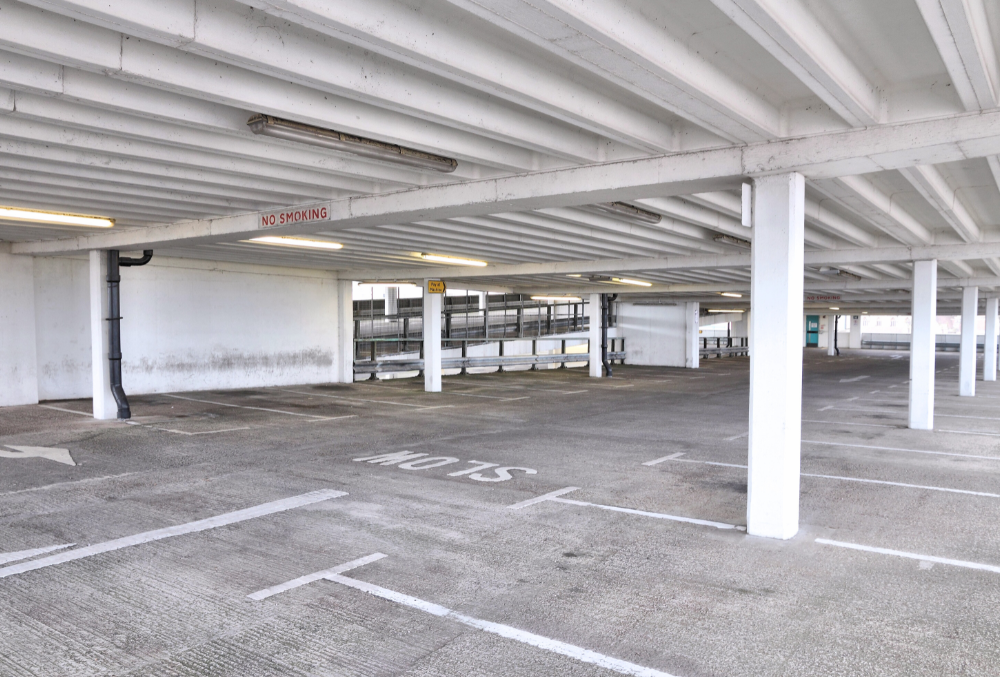
Polyurea polyaspartic floor coatings provide a wide range of benefits, establishing them as an excellent choice for both residential and commercial environments.
Their exceptional durability, impressive chemical resistance, and minimal maintenance needs make them stand out in the market.
Is It a Good DIY Project or Should You Hire a Professional?
Deciding whether to undertake the installation of polyurea polyaspartic floor coatings as a DIY project or to hire a professional involves several important factors, such as your skill level, the size of the area, and the performance outcomes you desire.
Understanding these considerations can significantly influence your overall satisfaction with the final result.
When evaluating the advantages and disadvantages of each approach, it’s crucial to keep a few key aspects in mind.
- Cost: While a DIY project may save you some money in the beginning, it is important to consider the expenses associated with the necessary tools and materials.
- Required Tools: Successfully completing a DIY project might require the purchase or rental of specialized equipment, which can quickly increase costs.
- Customer Satisfaction: Hiring professionals generally results in a polished and reliable finish, while a DIY approach provides the satisfaction of personal accomplishment.
Ultimately, both options have their merits, depending on personal preferences and individual circumstances, such as opting for epoxy floor coatings Atlanta.
A detailed installation guide can offer valuable insights, outlining essential procedures and guidelines that may lead to successful results, no matter which path you choose.
Key Differences Between Polyurea and Polyaspartic Coatings
The main distinctions between polyurea and polyaspartic coatings can be found in their chemical composition, performance durability, and curing times. These factors play a significant role in determining which coating is best suited for different applications.
What Are the Best Applications for Polyurea Polyaspartic Coatings? Exploring Polyurea Polyaspartic Atlanta, GA
Polyurea polyaspartic coatings are exceptionally versatile and can be utilized in a variety of environments, both commercial and residential, owing to their remarkable performance and durability.
These innovative coatings truly excel in areas where high traffic, flexibility, and resilience are essential. For example, in industrial facilities, their chemical resistance makes them particularly suitable for protecting surfaces from spills and harsh substances.
Likewise, automotive repair shops, warehouse floors, and food processing plants greatly benefit from the rapid curing capabilities and ease of maintenance these coatings offer.
Their ability to adapt to extreme temperatures and moisture levels enables them to perform well even in outdoor applications, where traditional flooring materials may struggle. With a blend of durability, aesthetic appeal, and safety features, these coatings effectively meet a wide range of flooring requirements.
How Do You Maintain and Clean Polyurea Polyaspartic Coatings?
Maintaining and cleaning polyurea polyaspartic coatings is crucial for ensuring their longevity and aesthetic appeal, particularly in high-traffic garage areas.
To achieve optimal performance and extend the lifespan of these surfaces, it is important to implement a systematic maintenance routine. First and foremost, regular sweeping or vacuuming should be prioritized to remove dirt and debris that could wear down the surface.
Using mild detergents and a soft-bristle brush with warm water, rather than harsh chemicals, can effectively lift stains without compromising the integrity of the coating, especially from oil spills.
It is also advisable to avoid abrasive cleaning tools, as they can scratch the surface and diminish its shine.
What Are the Costs Associated with Polyurea Polyaspartic Floor Coatings?
Understanding the costs associated with polyurea polyaspartic floor coatings is essential for assessing their value as an investment in your garage or commercial space.
When considering the financial aspects, it is important to take into account a few key factors. First, the cost of purchasing materials can vary significantly depending on the quality and brand you select.
Along with materials, you may require specialized tools that could necessitate further investment. Hiring professionals for installation will also contribute to the overall cost, but their expertise can ensure a flawless finish.
Here are some important considerations to keep in mind:
- Size of the area: Larger spaces naturally require more materials and labor, which will affect the total cost.
- Complexity of the installation: If the surface needs substantial preparation, such as repairing cracks or leveling with stamped concrete overlays, this will increase the overall price.
- Customizations: Any additional custom features you desire will further impact the budget.
By carefully evaluating all these elements, you can develop a detailed and accurate estimate for your project, transforming it into a success.
How Can You Tell If Your Floor Needs a New Coating Using Advanced Polyurethane Chemistry?
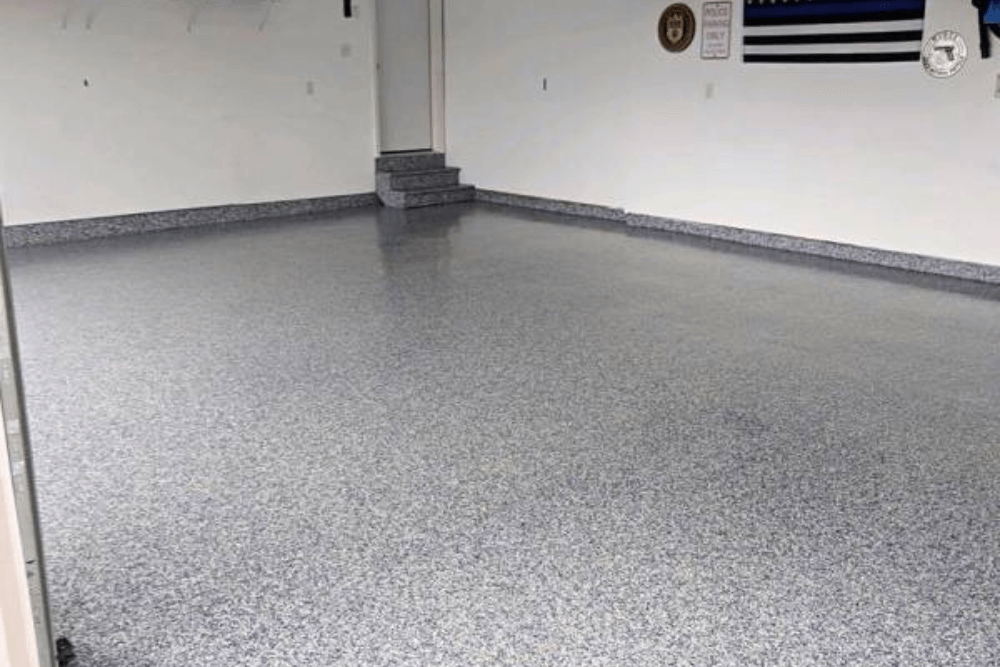
Determining whether your floor requires a new polyurea polyaspartic coating can be based on several signs, such as visible wear, a decline in its visual appeal, and signs of surface damage. Consider a difference comparison to assess these factors better.
As time goes on, certain indicators may suggest that a fresh coating is needed. For example, the appearance of cracks or chips may indicate that the existing layers are deteriorating.
Additionally, if you observe a noticeable reduction in slip resistance or if the surfaces start to feel rough or uneven, these could be clear signals that recoating is necessary.
When assessing the condition of your floor, consider the following points:
- Moisture issues: Look for evidence of moisture damage, such as discoloration or bubbling in the UV stable coating.
- Previous coating effectiveness: If the previous coating has begun to peel or fade significantly, it may no longer provide the level of protection it once did.
To evaluate your floor’s condition, it is advisable to conduct regular visual inspections to check for these warning signs. A simple water test—where droplets of water are placed on the surface to see if they bead up or soak in—can offer insights into how well the coating is performing.
Engaging in regular maintenance can extend the life of your floor and ensure it remains in optimal condition.